CSVN – VRG hiện có 65 công ty trồng cao su với tổng diện tích 407.800 ha trải dài khắp các vùng miền, Lào và Campuchia với 59 nhà máy, xưởng chế biến mủ với tổng công suất thiết kế 636.400 tấn/năm. Những năm gần đây, nhằm giảm chi phí sản xuất, hạ giá thành sản phẩm, giảm phát thải và bảo vệ môi trường, nhiều nhà máy chế biến cao su của các công ty thành viên VRG đang chuyển từ năng lượng truyền thống sang các nguồn năng lượng xanh, nhiên liệu sinh khối (Biomass).
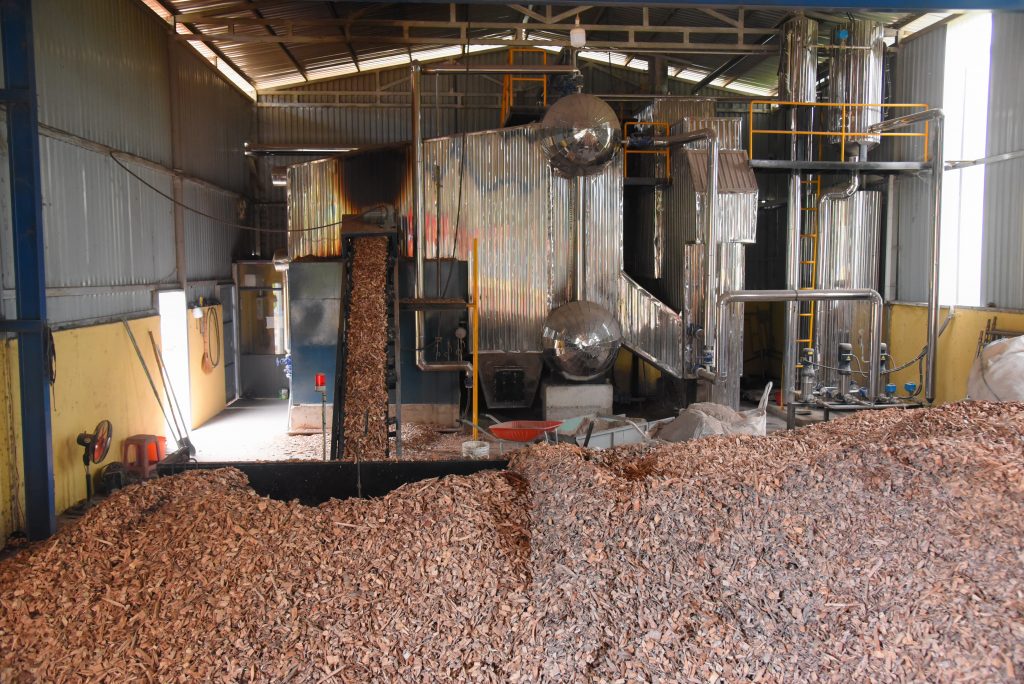
Chuyển đổi từ dầu, gas sang Biomass
Nhà máy chế biến của Công ty CPCS Bà Rịa trung bình mỗi năm chế biến gần 15.000 tấn mủ các loại như SVR10, SVR 5, SVR 3L, CV 50, CV 60… Trước đây, nhà máy cung cấp nhiệt lò xông từ nhiên liệu là dầu diesel. Từ tháng 9/2023, nhà máy đã chuyển đổi sang hệ thống sấy mủ với nhiên liệu sinh khối. Ông Nguyễn Văn Hoàng – Giám đốc Xí nghiệp Chế biến Cao su Bà Rịa cho biết: “Nhà máy đã đã đầu tư hệ thống cung cấp nhiệt lò sấy mủ với nhiên liệu đốt là dăm gỗ cao su. Với hệ thống sấy Biomass, công nhân dễ thao tác, vận hành hơn sấy dầu, nhiệt độ cũng dễ kiểm soát hơn”.
Còn tại nhà máy chế biến Công ty CPCS Hòa Bình, toàn bộ hệ thống xông sấy mủ bằng dầu DO đã được chuyển sang Biomass từ đầu năm 2023 và đang hoạt động ổn định.
Tại TCT Cao su Đồng Nai, ông Trần Văn Mạnh – Trợ lý GĐ Xí nghiệp Chế biến chia sẻ: “Để đáp ứng nhu cầu ngày càng cao của khách hàng, đồng thời chung tay bảo vệ môi trường, tăng trưởng xanh và phát triển bền vững hướng đến 3 mục tiêu quan trọng gồm: Phát triển kinh tế, bảo vệ môi trường, trách nhiệm với cộng đồng và xã hội, hiện các nhà máy chế biến của TCT đã hoàn thành kế hoạch chuyển đổi từ sấy mủ cao su bằng gas sang Biomass. Khi được cấp phép chính thức, các nhà máy sẽ sớm chuyển đổi sang nhiên liệu sinh khối để nâng cao hiệu quả kinh tế và bảo vệ môi trường”.
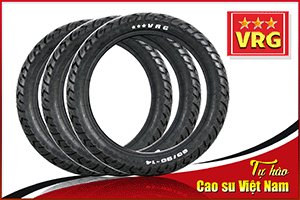
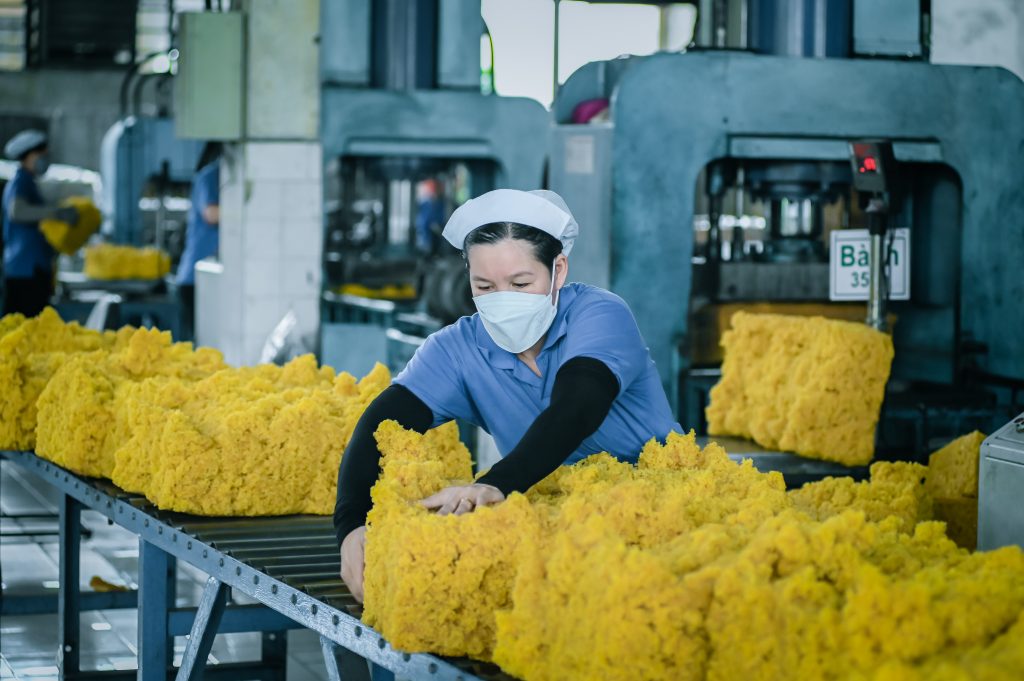
Nâng cao hiệu quả SXKD và bảo vệ môi trường
Trước đây, với hệ thống lò sấy bằng dầu DO, để sấy 1 tấn mủ tinh phải tiêu tốn 22 lít dầu, với mủ tạp phải tiêu tốn 33 lít dầu. Với hệ thống sấy Biomass hiện tại sẽ tiết giảm 20% chi phí nhiên liệu. Ông Nguyễn Văn Hoàng – Giám đốc Xí nghiệp Chế biến Cao su Bà Rịa chia sẻ, sau 3 tháng đưa vào hoạt động hệ thống sấy Biomass, chi phí vận hành tiết kiệm hơn 637 triệu đồng, chất lượng sản phẩm cũng ổn định hơn, mủ chín đều, màu sáng hơn.
“Các sản phẩm mủ sấy, đặc biệt là mủ cốm có yêu cầu chất lượng cao, trong khi hệ thống sấy bằng buồng đốt dầu với nguyên tắc đốt, cung cấp nhiệt trực tiếp đôi lúc nhiên liệu cháy không hết, bám dính vào sản phẩm, mủ sấy sẽ bị ám khói. Còn với hệ thống lò sấy Biomass phương pháp cung cấp nhiệt trung gian, công nghệ thu hồi và tái tuần hoàn nhiệt sẽ giúp chuyển hóa một cách hiệu quả năng lượng hóa học có trong nhiên liệu rắn thành năng lượng hơi nước để cung cấp cho lò sấy mủ cao su. Mủ sẽ chín đều hơn, thời gian sấy mủ nhanh hơn, công suất lò có thể tăng thêm 10% mà mủ vẫn chín tốt, chín đều hơn” – ông Lê Văn Hà – GĐ Nhà máy Chế biến Cao su Hòa Bình chia sẻ thêm.
Đặc biệt với mủ SVR3 có 2 chỉ tiêu quan trọng là Po và màu, khi sấy bằng hệ thống sấy Biomass, chỉ tiêu Po sẽ tăng lên và màu mủ sáng hơn. Với mủ CV thì chỉ tiêu PRI ổn định hơn. Từ đó nâng cao giá trị sản phẩm, đáp ứng nhu cầu ngày càng cao của khách hàng.
Việc chuyển đổi từ nhiên liệu dầu DO, gas sang Biomass đang được nhiều nhà máy tích cực thực hiện. Hiện Tập đoàn đã có 12 lò sấy chuyển đổi từ nhiên liệu dầu DO sang sử dụng lò đốt Biomass. Bên cạnh việc chuyển từ dùng dầu DO, gas… sang Biomass, nhiều công ty thành viên của VRG cũng đang đẩy mạnh sản xuất và sử dụng các nguồn năng lượng xanh khác, trong đó có điện mặt trời áp mái. Tổng công suất điện mặt trời áp mái toàn Tập đoàn tính đến hết năm 2022 là 10.112,25 kWp, tương đương với việc giảm phát thải 10.321,3 tấn CO2/năm.
ĐÀO PHONG
Related posts:
Lê Minh Trí - con công nhân Cao su Dầu Tiếng: Thủ khoa 2 khối trong kỳ thi Tốt nghiệp THPT năm 2022
Học và làm theo Bác là việc làm thường xuyên, tự giác
VRG trao giải báo chí viết về ngành cao su lần 4 năm 2024
Cao su Bắc Trung bộ: Vượt lên đại dịch Covid -19, phấn đấu hoàn thành kế hoạch
Đ/c Trần Công Kha - Bí thư Đảng ủy, Chủ tịch HĐQT VRG chúc Tết CBCNV LĐ
Cao su Phước Hòa: Top 50 công ty niêm yết kinh doanh hiệu quả nhất Việt Nam giai đoạn 2011 - 2022
Tối ưu hóa năng suất vườn cây tái canh: Cần những yếu tố gì?
"Xuân này anh không về"
Phát huy truyền thống đoàn kết, đưa nông trường vững bước đi lên
Đảng viên giàu nhiệt huyết và đam mê nghiên cứu