CSVN – 31 năm gắn bó với Xí nghiệp Cơ khí Vận tải (TCT Cao su Đồng Nai) là khoảng thời gian nhiều thăng trầm nhưng hạnh phúc đối với Thạc sỹ Hoàng Văn Trung – Phó Giám đốc Xí nghiệp. Đây là nơi anh và đồng nghiệp được thỏa sức thực hiện đam mê sáng tạo, tạo dấu ấn riêng, làm lợi hàng tỷ đồng mỗi năm cho đơn vị.

Tâm huyết với nghề
Một chiều cuối tháng 7, chúng tôi đến xí nghiệp tìm gặp anh để hiểu sâu hơn về công việc, về niềm đam mê sáng tạo. Anh đang tất bật bên chiếc máy tính, hoàn thiện công đoạn cuối bản vẽ di dời mặt bằng nhà máy chế biến Long Thành, thuộc TCT Cao su Đồng Nai. Rồi anh lại chạy sang phân xưởng hướng dẫn anh em công nhân gò hàn, sửa máy.
Trò chuyện với chúng tôi, anh Trung chia sẻ, suốt 31 năm công tác tại Xí nghiệp, với lợi thế là một thạc sỹ chuyên ngành cơ khí chế tạo máy, anh luôn suy nghĩ, tìm tòi các giải pháp làm lợi cho đơn vị, giảm sức làm việc nặng nhọc cho công nhân. “Trong quá trình công tác, tôi thấy những thiết bị chế biến nhập từ nước ngoài trước đây rất mắc, tốn nhiều chi phí của công ty.Qua xem xét, thấy những thiết bị này mình hoàn toàn chế tạo được. Suốt thời gian dài, tập trung vào nghiên cứu và sau một thời gian chúng tôi đã chế tạo thành công nhiều thiết bị quan trọng.
Ví dụ lò sấy công suất 2,5 tấn/giờ, đây là thiết bị khó nhất trong tất cả các thiết bị chế biến cao su, chúng tôi đã làm được vào khoảng năm 2000. Xuất phát từ thành công đó, tôi và đồng nghiệp đã thiết kế và chế tạo nhiều loại máy. Đến nay, hầu như tất cả thiết bị chế biến cao su của TCT Cao su Đồng Nai chúng tôi đều thiết kế và chế tạo được, chỉ trừ máy chế biến cao su ly tâm”, anh Trung cho biết.
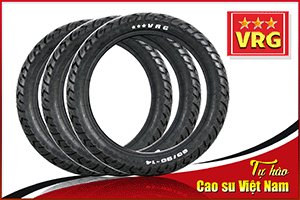
Trong tất cả những thiết bị mà anh Trung thiết kế, chế tạo, anh tâm đắc nhất giải pháp thiết kế chế tạo lò sấy cao su công suất 2,5 tấn/giờ. So với lò sấy nhập ngoại, lò sấy do anh chế tạo có rất nhiều ưu điểm về giá thành, tuổi thọ, nổi bật là tiết kiệm nhiều nhiên liệu. “Với sản xuất mủ tinh, lò sấy chúng tôi sản xuất tiêu hao nhiên liệu khoảng 23,5 đến 24 lít dầu DO/tấn sản phẩm, còn lò sấy do Malaysia sản xuất tiêu hao từ 28 đến 29 lít dầu DO/tấn sản phẩm. Còn sản xuất mủ tạp, tiêu hao nhiên liệu chỉ khoảng 30 đến 31 lít dầu DO/tấn sản phầm, lò sấy Malaysia tiêu hao từ 37 đến 38 lít dầu DO/tấn sản phẩm.
Với những kết quả đạt được nói trên, ngoài việc giảm giá thành chế tạo, sẽ tiết kiệm chi phí nhiên liệu mỗi năm 460 triệu đồng đối với dây chuyền mủ tinh, 800 triệu đồng với dây chuyền mủ tạp. Đây là con số rất có ý nghĩa trong thời điểm mà giá bán cao su rất khó khăn như hiện nay”, anh Trung phân tích.
Tạo thương hiệu đặc trưng cho đơn vị
Ngoài ra, anh Trung và đồng sự còn thiết kế, chế tạo thành công nhiều loại máy khác, như: Máy nhai mủ đất công suất 300 kg/giờ, giá trị làm lợi ước tính 100 triệu đồng/năm; máy ép 100 tấn; máy ép bành mủ cốm; chế tạo mới hệ thống xử lý mùi lò sấy mủ tạp….. ước tính giá trị làm lợi cho công ty hàng tỷ đồng mỗi năm.
“Bản thân tôi và đơn vị rất quan tâm đến công tác nghiên cứu, thiết kế và sáng tạo. Việc làm của chúng tôi còn nhận được sự đồng tình, ủng hộ rất lớn của lãnh đạo xí nghiệp, lãnh đạo TCT. Lãnh đạo cũng mong muốn xí nghiệp tạo được sản phẩm đặc trưng riêng để tạo thương hiệu. Đến nay, tất cả thiết bị do Xí nghiệp thiết kế, chế tạo đảm bảo về mặt thẩm mỹ, chất lượng, ưu thế kỹ thuật. Thiết bị được thiết kế, chế tạo tại chỗ, nên giá thành thấp so với nhập ngoại. Nhờ vậy sản phẩm của xí nghiệp nhận được sự tin tưởng của khách hàng”, anh Trung chia sẻ.
Bài, ảnh: Bình Nguyên
Related posts:
"Nên nuôi dưỡng và nhân rộng gương điển hình tiên tiến"
Vươn lên từ ý chí và nghị lực
Công nhân người Campuchia đạt sản lượng gần 17,3 tấn mủ/năm
Chúng tôi luôn ở bên các bạn
Càng khó khăn càng gắn bó với ngành
Không ngủ quên trên truyền thống
Phan Thị Doanh - Nữ công nhân làm tròn cả hai vai
Mô hình khoán vẫn phát huy giá trị
Một lòng theo nghiệp cao su
Quan tâm, chăm lo nhiều hơn để giữ chân người lao động